China's aluminum processing industry is equipped with the most advanced equipment
Dong Xing
Dong Xing
2018-07-10 10:39:26
Since more than 80% of China's aluminum processing industry equipment has been built since the beginning of the new century, and most of them are imported machines from the world's top manufacturing companies such as Wagstaff, the extruder of Japan Ube Industries Co., Ltd. , Germany's SMS Group's strip mill, heavy-duty extruder, reverse extruder and thick plate pre-stretching machine, Austrian Oberna company's heating furnace and heat treatment furnace.
- Smelting holding furnace group. There are about 95 sets of the world's top aluminum alloy smelting-heating furnaces, with a capacity of about 2,600 tons. It has the advantages of energy saving and environmental protection. The energy consumption is less than 55m3/ton of aluminum natural gas. The greenhouse gas and dioxin emissions can meet the requirements of the European Economic Community. Environmental regulations require.
——The casting machine sets the world's advanced Dacheng. As of 2017, China has about 4,500 round ingot and flat ingot casting machines. The largest round ingot casting machine can cast 160 pieces at a time. The flat ingot casting machine can cast a single ingot with a mass of 42 tons. The maximum length of the ingot is 9m, which can be listed as a world record. There are 48 Wagstaff round ingot casting machines introduced in China, among which Liaoning Zhongwang Aluminum Co., Ltd. has a total of 13 units, with a total production capacity of 1.2 million tons/year. This is unique in the world. Nearly 90 sets of slab casting machines have been introduced in China, including 55 of Wagstaff, and 4 of Almex, which are dedicated to casting aerospace hard alloy slabs. A casting machine that can cast both ingots and ingots (ingot/billet).
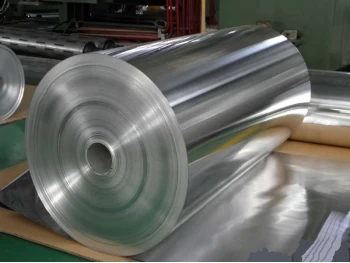
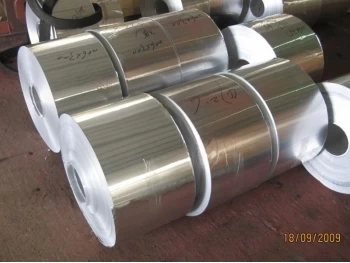
- Ingot hot rolling (plate hot rolling). China's aluminum sheet hot rolling began in 1919, using two-roll small hot rolling mill to roll iron mold casting small flat ingots, producing small plates, modern aluminum strip rolling began in November 1956. Northeast Light Alloy Co., Ltd. 2000mm four-roller irreversible The hot rolling mill was put into operation, and the equipment was imported from the Soviet Union. In 1970, Southwest Aluminum (Group) Co., Ltd. was completed and put into production. There is a 2800mm four-roller irreversible hot rolling mill with full independent property rights in China, which is made up of the first heavy machine. Manufacturing Co., Ltd. design and manufacture.
The ingot is heated before hot rolling, and this process is often referred to as preheating. Hard alloy ingots must be homogenized before machining. Homogenization is a time-consuming and energy-intensive process. Preheating is also possible. Homogenization and preheating can be carried out separately or in combination. China's aluminum(1235 aluminum foil wholesales) strip rolling industry has the world's most advanced and most advanced propulsion furnace. The furnace has the advantages of uniform heating temperature, fast heating speed, energy saving and environmental protection, easy automatic control, and large capacity.
As of 2017, there were 52 slab-type propelling furnaces and homogenization furnaces imported from EBNER and other companies in China, and 85 domestically produced furnaces. Nanshan Light Alloys Co., Ltd. has five HICON push-type heating furnaces, each of which can hold 25 tons of slabs of 30 tons. It is the world's largest production line with the largest loading capacity and the largest amount of material. The EBNER push-type heating furnace of Tianjin Zhongwang Aluminum Co., Ltd. soft alloy hot rolling line can hold ingots with thickness 390mm~650mm, width 1240mm~2700mm, length 4500~8000mm, ingot temperature uniformity ±3°C, thermal efficiency ≥72 %, the billet heating temperature is 350 ° C ~ 620 ° C, the maximum(Aluminum battery foil manufacturer) mass of a single ingot is 26.5 tons, up to 25 pieces.
In 2017, China's aluminum strip hot rolling mill and production line are shown in Table 2. The hot tying line refers to the production line of ≥ 2 racks of finishing mills. The total production capacity of hot rolled strips is 17.91 million tons/year, accounting for about 5.3% of the world's total production capacity. In the hot rolled strip, the output of the thick plate generally does not exceed 8%, and the rest is a coil blank for cold rolling, and the thickness of the hot rolled strip for cold rolling is usually ≥ 2.2 mm.10